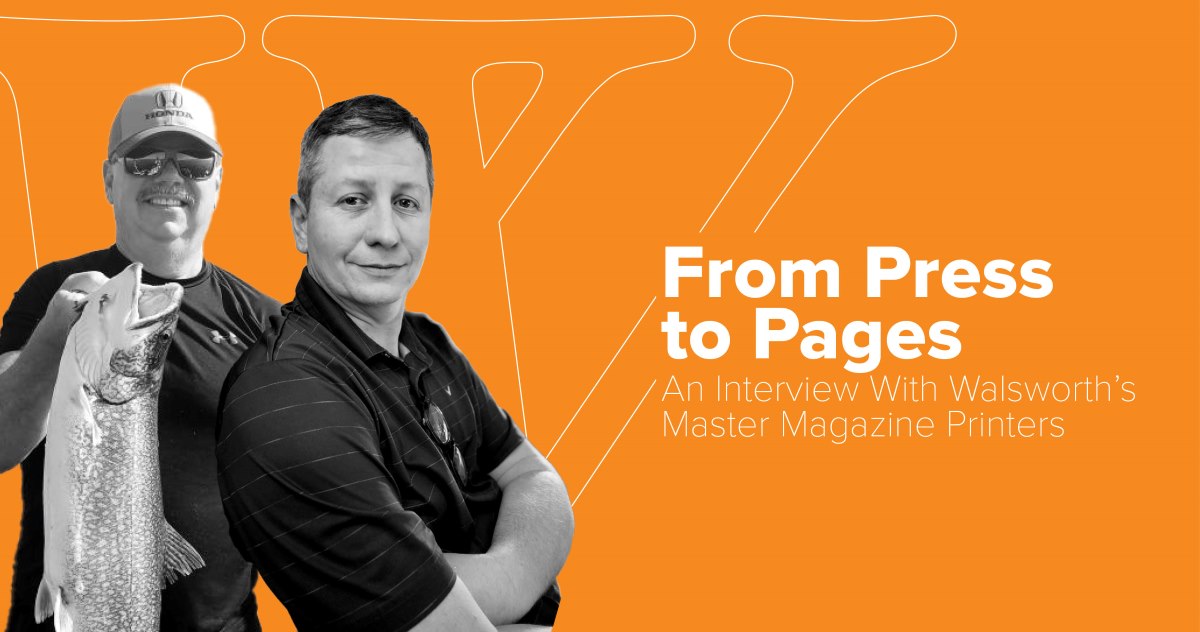
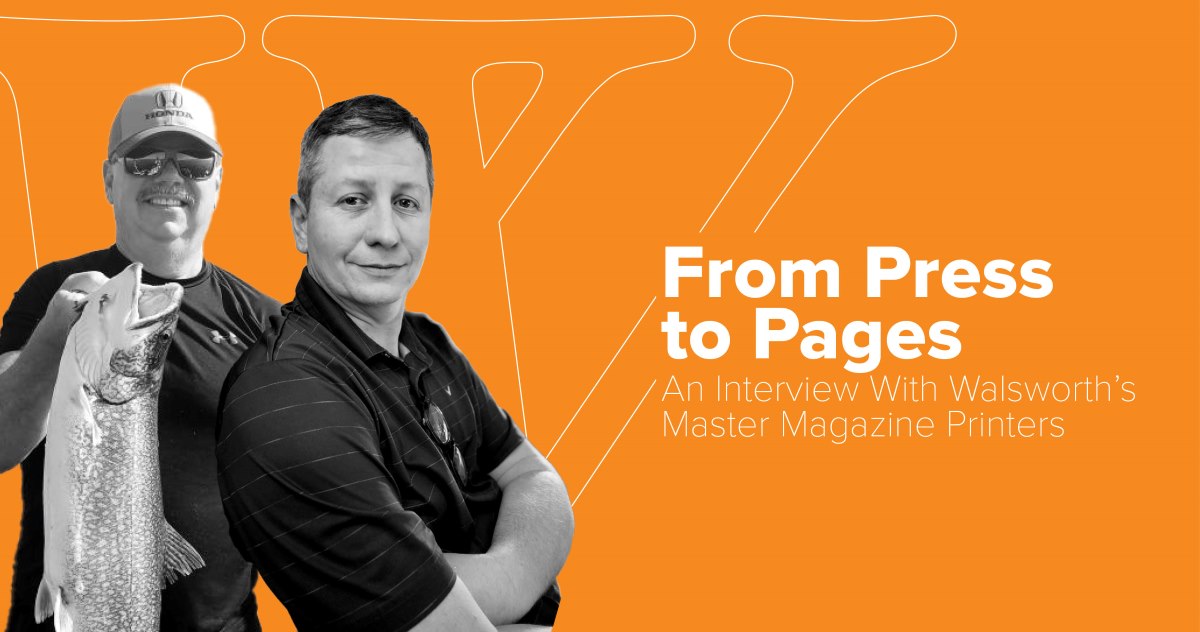
As a printing company with 87 years of experience, there’s a lot of skill and knowledge amongst our talented staff. We sat down for a conversation with two of our master magazine printers; Phil Archer, General Manager at Walsworth – Saint Joseph, and Jack Maddox, Press Manager at Walsworth – Fulton, to find out more about their thoughts on the print industry and what it takes to print magazines.
How It All Started
Maddox and Archer share a common trait: their humble beginnings in the print industry. Both men started in print right out of high school in an entry-level role. “A friend of mine suggested working at the Ovid Bell Press; I was hired on and started right around my 18th birthday,” said Maddox. “Then, I was a Sheetfed Operator for about a year. I went from there to Web Operator, and after that, I took the foreman job on nights for about 12 years. After that, I worked as the Bindery Manager, then Night Shift Lead in the press room before I got the management spot about two and a half years ago.”
While Maddox has worked in print for around 25 years, Archer boasts a four-decade career in print. “It’s scary to think this is actually my 41st year in the printing industry,” said Archer. “I started out of high school in 1983 as a utility in the press room at RR Donnelley, sweeping the floors and dumping trash, working my way up to Press Operator there. I was there for 11 years.” He then worked foreman, supervisor and management roles at several printing companies in plants across the country, including Denver, Colorado; Clarksville, Tennessee; Jefferson City, Missouri; and Roanoke, Virginia, before taking the manager position in Saint Joseph in 2017.
How It’s Changed
It’s no secret that thanks to technology, the world has changed drastically in the last few decades, and the print industry is no exception. “When I started in the trade, pre-press was still stripping film and burning plates, now that’s all computer to plate,” said Maddox. “You had to key ink by hand, now it’s all automated. The industry has changed a lot in the last few decades.”
Archer adds, “When I first got into the industry, color controls and register systems were all done manually. Now there’s newer design equipment, gapless technology on our blankets, computer to plate – it’s all digital now. It’s reduced errors and increased productivity. In the bindery, with our new binder, everything is set up automatically. We’ve seen increased uptime with the design of new pockets and increased speeds for that same reason.”
The Day-to-Day
Maddox’s typical day as Press Manager looks a little different at the moment, thanks to Walsworth – Fulton’s current push to install newer equipment. “Right now, I’m mostly dealing with equipment installations, searching for parts for this new equipment or trying to make new contacts with vendors,” said Maddox. “Overall, I’m trying to get my department to give the next department the best product we can. It can be challenging because a lot of this stuff is hard to come by. But looking toward the end of the tunnel, I know everything is going to be great.”
Up in Michigan, Archer went through a similar challenge when he first started at Walsworth – Saint Joseph seven years ago. “When I first got here, the plant needed a lot of change. We had older equipment that needed to be maintained and replaced. Getting a job in and out the door required a different effort and focus than we have today,” said Archer. Thankfully, that light at the end of the tunnel arrived. “Today, we’ve got processes in place. I might have spent more time with quality issues in the past. We don’t have many of those anymore. My typical day today is, I catch up on emails and do a standard meeting in the morning to find out what we’ve done in the last 24 hours and what we’re going to do in the next 24 hours.”
Their Love of Print
Archer cites the variety his job provides as a reason he’s stayed in the print industry for four decades. “One of the things I always wanted to do was come in every single day and it be different. It’s never the same, there’s always something different; you’re making something different. Different content, different paper, different challenges. It’s constantly challenging you. That’s something I enjoy. The next problem that needs to be solved.”
Maddox noted the combination of skills needed to be successful as a reason he loves working in print. “There’s a lot of hands-on work, and a lot of technology is involved. It’s a broad spectrum of things someone needs to know.”
Tips for Magazine Publishers
Over the years, Phil Archer has worked with countless magazine publishers, whether they’re first-timers or veterans of the industry. His advice? Understand the product you’re trying to create. “Take advantage of our onboarding process to understand how your design is going to look on press. Are you using the right paper? For example, if you have photographs, you don’t want matte stock, you want nice gloss,” said Archer.
Archer continued to emphasize the importance of considering what the item will be used for. “Is this a coffee table book, or something that people are only going to read once? If it’s a coffee table book, consider perfect bound or case bound. Saddle stitch is a great way to save money, but it doesn’t have the same longevity.” Having knowledgeable printers in your corner to help you with these decisions can be a game changer.
What You Should Know About the Print Industry
As a four-decade veteran of the print industry, Archer wants the world to understand that print is thriving. “It’s over a 70 billion dollar industry. It’s a big industry, but also close-knit,” said Archer. “It’s all over the world. It’s kind of like being a doctor; you can go all over the world and have a job in just about any city, anywhere you want to go there’s work to be done.”
Finally, Archer stressed the benefits of a career in printing. “There’s opportunity for advancement at all levels. If you don’t have a degree, you can still make it to plant manager. You can learn to be a supervisor. You can keep learning new roles. There are always opportunities for advancement and increases in pay.” Archer added, “For someone coming out of high school and college is not an option for them, the printing industry is alive and well. It’s gonna be there for a long time. To come in and learn a trade and have a career with the opportunity for advancement is a fantastic way to raise your family. We can help with that.”
Consider a Career in Print With Walsworth
If you’re interested in starting or continuing your career in print, Walsworth is a great place to learn the ins and outs of the trade. Walsworth has state of the art printing facilities in Saint Joseph, Michigan; Ripon, Wisconsin; and Fulton, Brookfield and Marceline, Missouri. Our company culture emphasizes trust, teamwork and integrity, and we’re passionate about hiring local talent from the communities that house our printing facilities. Browse our open positions and launch your career in print today!