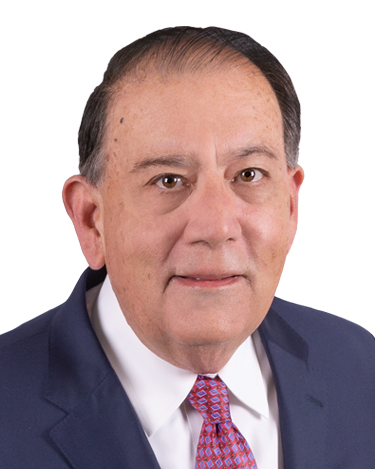
As Chief Operating Officer, Jim Mead plans and directs all aspects of the organization’s strategy and operational policies, objectives and initiatives. Jim relies heavily on his extensive experience and judgment to plan and accomplish goals, using a wide degree of creativity and latitude to lead and direct.