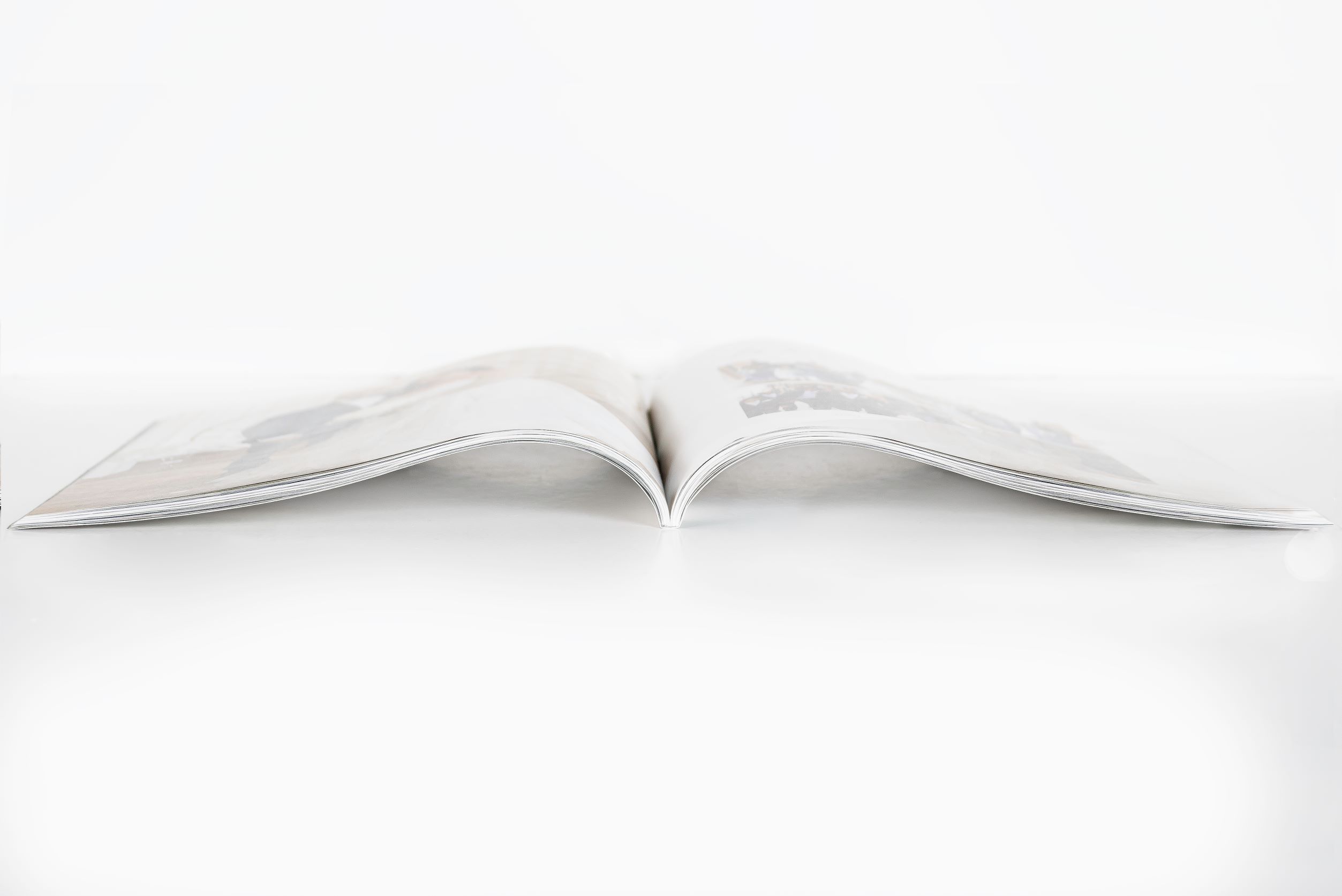
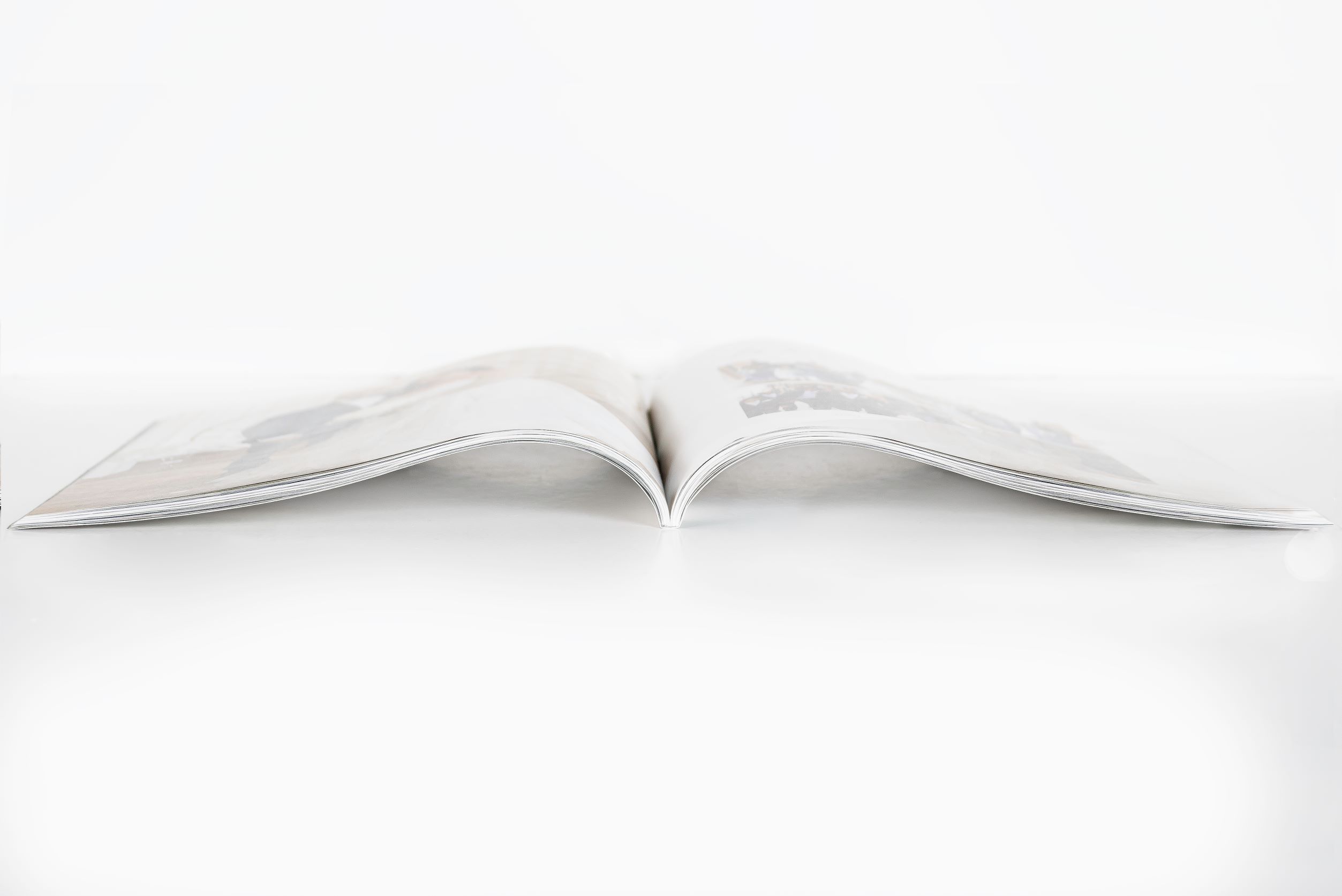
There’s so much more to binding than just paperback or hardcover. From the look to the weight to the longevity of the finished publication, it’s important to know how each binding technique can suit the unique needs of your publication and differentiate you from the competition.
In this series, we explore how different binding processes are performed in a commercial setting and how they affect the final product.
What is perfect binding?
Perfect binding, also known as soft cover binding, refers to a binding process in which the inside pages of a publication are ground down and glued at the spine before a soft cover is attached. Afterward, the cover and pages are trimmed on the non-spine sides to produce a publication with a clean, “perfect” edge.
Assembly required
The industrial construction of a perfect bound publication varies between machinery and binderies, but the basic process in a perfect binding line is as follows.
After the inner pages of a publication are printed and folded into signatures, a gatherer sorts them in the correct sequence to create what is called a book block. The book block is then compressed in a clamp, which carries the publication spine-side down as it moves through the binder. The clamp glides the book block across a backbone saw which removes the signature folds and grinds the spine. The spine is ground down, notched and roughened with brushes or sandpaper which exposes paper fibers and increases the surface area of the backbone so the side glue can adhere more effectively.
Still spine-side down, the book block is carried through the gluing station. Many perfect binders use a type of hot-melt adhesive for the spine glue called polyurethane reactive, or PUR glue. Applicator wheels roll the PUR glue from heated glue pots up onto the spine of the publication.
Side glue is applied following the spine glue, as a combination of hot-melt adhesives with varying viscosities is often used for perfect binding. The PUR glue used for the spine can be followed with a different hot-melt adhesive for the side of the spine to adhere to the cover. Hot melts are comprised of a mixture of resins and polymers that bond in high temperatures and reach a solid state when cooled. A metering roller is used during the gluing process to remove excess glue and ensure the adhesive covers the backbone fully and evenly.
Once the glue is applied to the book block, its cover is fed through a separate track where a feeding mechanism scores the inner spine at the width needed for the cover to fold neatly around the book block.
After hot-melt adhesive is applied, the track carrying the scored cover rises to meet the spine of the clamped book block. While the front, back and sides of the book block are held firmly in place, the cover is pressed onto the backbone and the nipping station clamps the spine on the hinge scores, holding for a moment to allow the glue to seep fully into the backbone.
The untrimmed publication is then placed on a conveyor belt on its way to the trimmer. The length and speed of the conveyor belt is designed to last the exact amount of time required for the adhesive to dry enough for trimming. For traditional hot-melt adhesives, this initial dry time only lasts 45 seconds, but the adhesive takes about eight hours to dry completely.
The trimming unit takes the most time per product compared to the other processes in a perfect binding system, so some binding systems deliver overflow product to a stacker for off-line trimming. For on-line trimming, the conveyor belt delivers the publications directly into the trimmer, where three large blades descend upon the three unbound edges of the publication, also known as the head, foot and thumb edge. This process removes the remaining signature folds and cover edges, leaving behind a clean-cut, perfect-bound final product.
Use cases for perfect-bound products
Because perfect binding is the only softcover binding method that allows for printing on the spine, it is a popular choice for publications which are likely to be stored on shelves. While it costs more than some other paperback binding methods, perfect binding is great alternative to hardcover or case binding economically. Perfect binding also works well for a wide range of page counts and paper types, so it is a flexible option for many titles.
However, perfect binding is not always the perfect choice for any given publication. While this binding type works well for publications between .125 to 2.25 inches thick, printed items with thinner or thicker backbones than this can jeopardize the integrity of the spine and result in a less durable product.
Perfect binding does not allow a publication to lay flat like Smyth sewn or coil bound publications. This should be taken into consideration for any publications requiring hands-free reading, such as instruction manuals or cookbooks.
Because the cover of the spine is glued directly to the book block, the pages of a perfect-bound publication require larger margins, leaving less space available for design. The marginal space allotted for the glue and content that could fall into the gutter usually adds up to a necessary margin of .5 inches on all edges, which is double the size of margins needed for other binding types.
Weighing the options
Perfect binding allows for a desirable balance of durability and design, as the glue used during binding offers product longevity and the final trim lends to a clean, professional look. Perfect binding is often chosen for books, magazines, catalogs, journals and other publications when a durable yet flexible, attractive and sleek final product is desired. If perfect binding is the best choice for a publication, the result is a beautiful and long-lasting product that will be enjoyed for many years to come.
If you are considering perfect binding for your next print project with Walsworth or you would like to speak with someone, our knowledgeable staff can help find the best option for you!