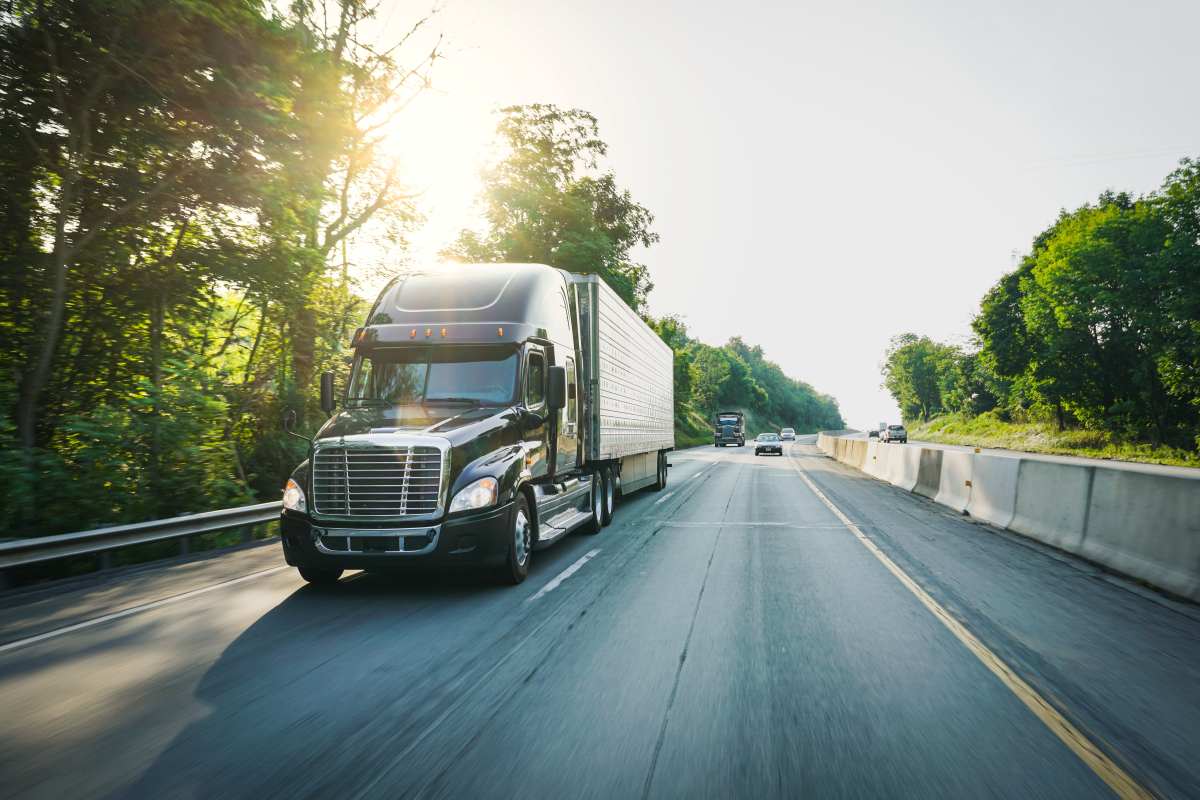
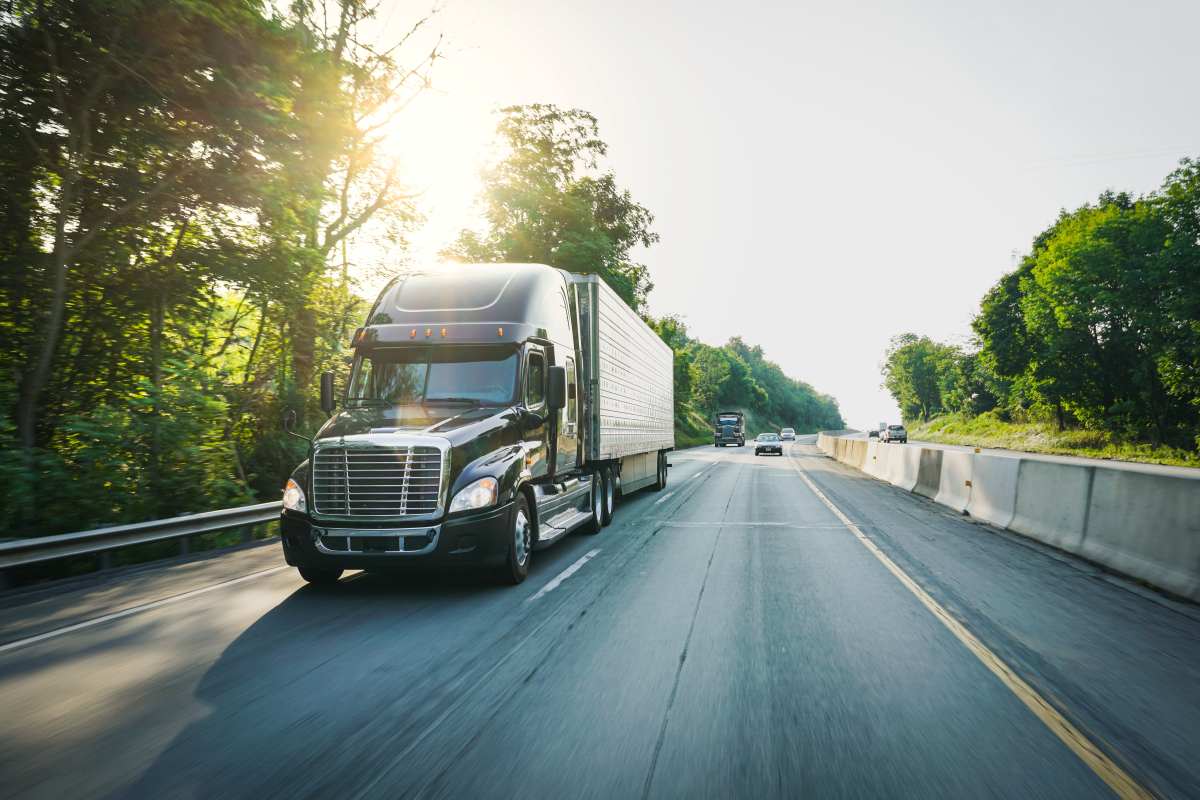
The fulfillment process for print magazines, catalogs and books can be a complex and time-consuming task with lots of room for errors. Getting your print products into the hands of your customers in a timely manner is crucial for maintaining your brand’s image – fulfillment errors can lead to delays, errors and dissatisfied customers.
This blog will give tips on how to streamline your print fulfillment process, helping you avoid errors and find ways to consistently deliver your publications on time and within budget.
What Is Print Fulfillment?
Print fulfillment is the process of receiving, storing and shipping printed materials to customers. Engaging content, beautiful design and high-quality printing are all crucial considerations, but your customers won’t get to enjoy your publications if they never make it to their doors. Publishers may choose to receive their printed products and store them in warehouses, shipping them to customers as they’re ordered, or they may partner with a printing company that offers in-house fulfillment.
The Challenges of Print Fulfillment
Managing print fulfillment involves multiple moving parts, including warehousing, inventory management, order processing, shipping and even handling returns. Without a seamless system in place, these elements can quickly become overwhelming, leading to delays, errors and excessive costs. Businesses often struggle with:
- Storage and inventory management: Keeping track of printed materials and ensuring stock levels are optimized to meet demand.
- Order accuracy and speed: Efficiently processing and shipping orders to customers without delays or errors.
- Handling reorders and returns: Managing unexpected demand spikes or handling returned items effectively.
- Logistics coordination: Choosing the right shipping partners and methods to ensure timely deliveries at the best possible rates.
Tips for Publishers to Streamline Fulfillment
Here are several strategies you can implement to improve efficiency of your fulfillment process:
- Invest in Inventory Management Software: Implementing a robust inventory management system can help you track stock levels in real time, prevent over-ordering or understocking and automate reordering when needed.
- Optimize Your Warehouse Layout: Organizing your warehouse for efficiency – grouping similar items together, clearly labeling sections and reducing unnecessary movement – can significantly improve order fulfillment speed and accuracy.
- Standardize Packaging Processes: Establishing clear packing procedures and training employees on best practices will minimize mistakes and reduce processing time.
- Use Automation Where Possible: Consider using software to automate repetitive tasks such as label printing, order processing and tracking updates to improve efficiency and reduce opportunities for human error.
- Stay Up to Date on Mailing: Postal regulations are constantly changing. Make sure you’re well-informed on the best shipping practices for your specific business so you can take advantage of the most efficient options available.
- Create a Clear Returns Policy: Having a well-documented and simple return process will make it easier for customers and reduce the burden on your team when handling returns.
How Walsworth Simplifies Print Fulfillment
As a trusted print partner, Walsworth offers a one-stop solution that integrates printing with seamless fulfillment capabilities. Our streamlined approach ensures businesses and publishers can focus on what they do best – creating great content – while we handle the complexities of getting products into customers’ hands.
1. Warehousing and Inventory Management
With Walsworth’s warehousing solutions, businesses can store their printed materials in a secure and organized environment. Our advanced inventory management system tracks stock levels in real time, helping you avoid overstocking or running out of key publications.
2. Efficient Pick-and-Pack Operations
Accuracy and speed are essential in fulfillment, and Walsworth’s pick-and-pack operations are designed for precision. Our team carefully selects and packs each order, ensuring customers receive the correct items. Whether you’re shipping bulk orders to retailers or individual copies to subscribers, our fulfillment process is tailored to meet your needs.
3. Seamless Order Processing and Shipping
Walsworth integrates with multiple order processing systems to ensure smooth and efficient transactions. Our shipping and mailing expertise allows us to offer cost-effective delivery solutions, reducing transit times while keeping costs manageable. With tracking capabilities, you and your customers can stay informed about shipment status.
4. Hassle-Free Reordering and Returns
Demand fluctuations are a natural part of business, and Walsworth makes it easy to restock your materials when needed. We provide reports to inform you about inventory levels so you know when to reorder, ensuring your publications are printed and shipped without unnecessary delays. Additionally, our streamlined returns process helps manage customer returns, keeping inventory levels accurate and reducing waste.
Experience The Walsworth Difference
Print fulfillment doesn’t have to be a stressful and time-consuming process. With Walsworth’s comprehensive solutions, businesses and publishers can enjoy a streamlined, cost-effective and hassle-free fulfillment experience. Let us take care of the logistics so you can focus on growing your brand and delivering exceptional content to your audience.In addition to offering intelligent fulfillment solutions, Walsworth is a renowned magazine, catalog and book printer with over 88 years of experience. We pass the benefits of that expertise onto our customers, providing high-quality print solutions with state-of-the-art technology. Ready to simplify your print fulfillment process? Contact Walsworth today to learn more about the Walsworth difference.
* This article was developed with assistance from OpenAI’s GPT-4 large language AI model.